Process Optimization
In the globally competitive market place, Process industries look for ways of finding the most optimal path to producing the output that will provide them the extra edge to stay ahead.
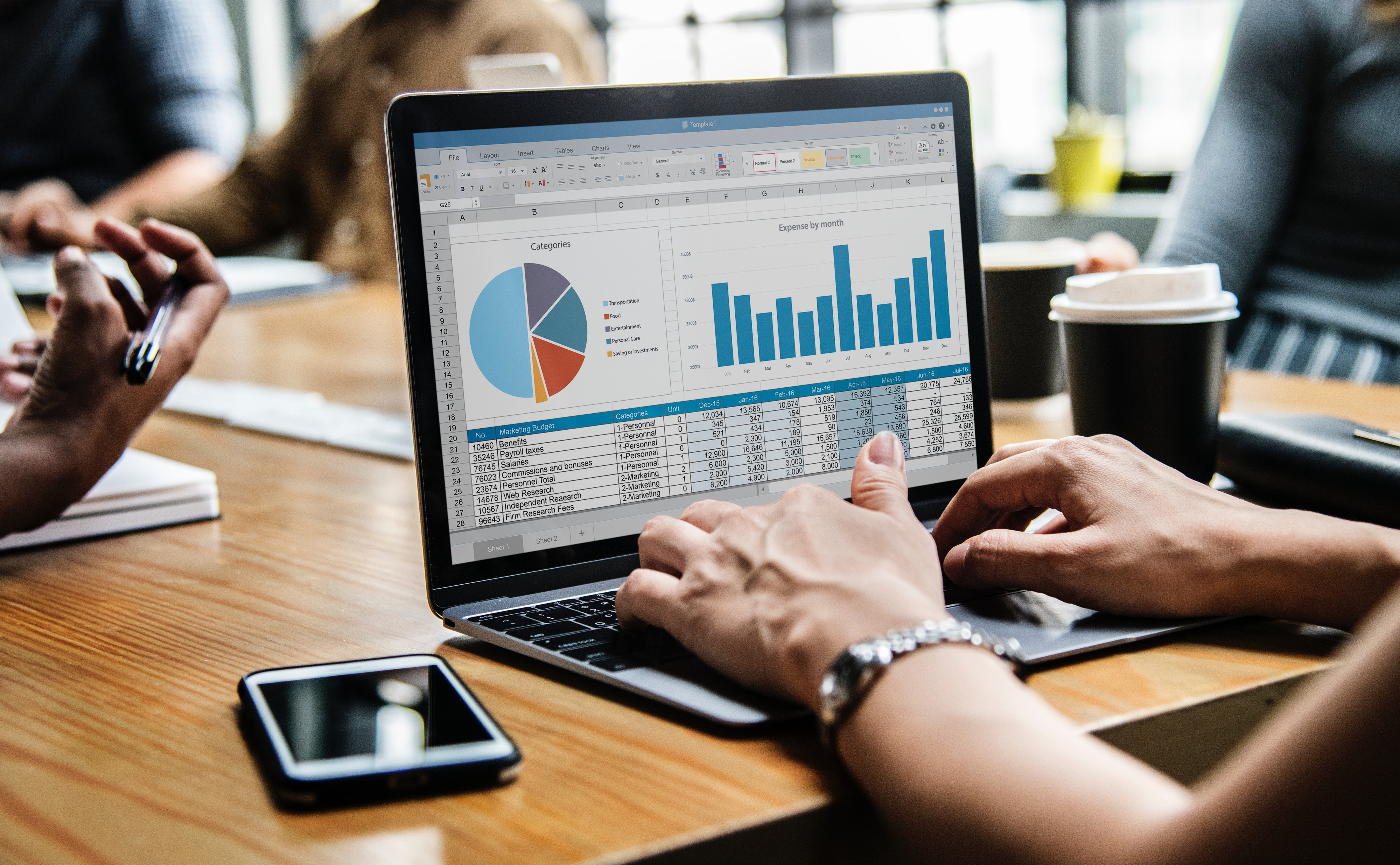
The generic ways to achieving this goal lie in three broad categories, namely improved workflows, operational efficiencies from existing processes and benchmarking to the best in the industry.
Process industry operations can be highly complex and integrated. Factors that can cause process upsets include variations in the feed, power outages, shut-downs of individual units etc. Upsets generally start small and cascade through the inter-connected operations to propagate and enhance in amplitude, creating more and more operating challenges. Process upsets can lead to off spec products, higher operational costs, and even environmental damage in extreme cases.
Beacon Solutions has a very experienced cross functional team to provide you the support needed to achieve these optimization goals. Our engineers will work with your team to develope a balanced systems approach to operations that is specifically designed to dampen these upsets, by identifying and eliminating the root causes
We recognize the fact that Process owners are looking for continuous improvement as far as yield is concerned, so they can remain competitive in a dynamic environment. The drive for improving existing workflows though, is often tempered by a perception of risk in charting a new course. The leadership at Beacon Solutions has a wealth of experience to enable its clients make a considered decision when it comes to process optimization.
The concept of process optimization typically begins with initial interaction with the client side leadership team to assess the organizational goals, as well as areas of concern. We apply this understanding to plan an audit of the current processes and outcomes, in order to identify opportunities for improvement. The key aspects of the audit include the following:
- Identification of the main processes from Input to Output
- Key Performance Indicators (KPI) for the various processes
- Understanding of Cause and Effect relationships
Based on the assessment from the audit, our team of experts uses their benchmarking experience and software tools to come up with a definition of an Improvement Action Plan, linked to organizational goals and concerns.
Engaging with the client side leadership team at this stage is critical to the next phase of the project to get an intuitive feel for the focus areas.
Once the Process Optimizations sub projects are clearly defined, our team at Beacon Solutions prepares the estimations of the budget and the scope of the project/s. Timelines are clearly defined as well, up to a level 2 schedule. The project at this stage is ready for approval by the Management, for allocation of budget and planning for the implementation stage.
Examples of typical projects may include the following:
- Cutting down production process steps or stages
- Debottlenecking to increase capacity
- Improvement in Performance Monitoring
- Production Planning refinements
- Improvement in efficiency of existing processes
- Process unit monitoring and alarms
- Integration of complex processes
- Leaner inventory of raw materials and finished goods
- Product quality improvement
- Improvement in logistics and transportation for supply chain optimization
- Reduction in waste generation
The Beacon Solutions team is also available to help in the implementation phase, starting with the selection of single or multiple contractors. Supervision services for the implementation are available on call as needed, to ensure the success of the entire project. This will include the process of overseeing project progress to ensure that the solutions which were identified are adapted to the existing systems and workflows, staff and workers are trained and brought up to speed early, and monitoring and control functions are implemented.
The Beacon Solutions team works alongside the client team at every step till the project is successfully closed and the fruits of process optimization realized.